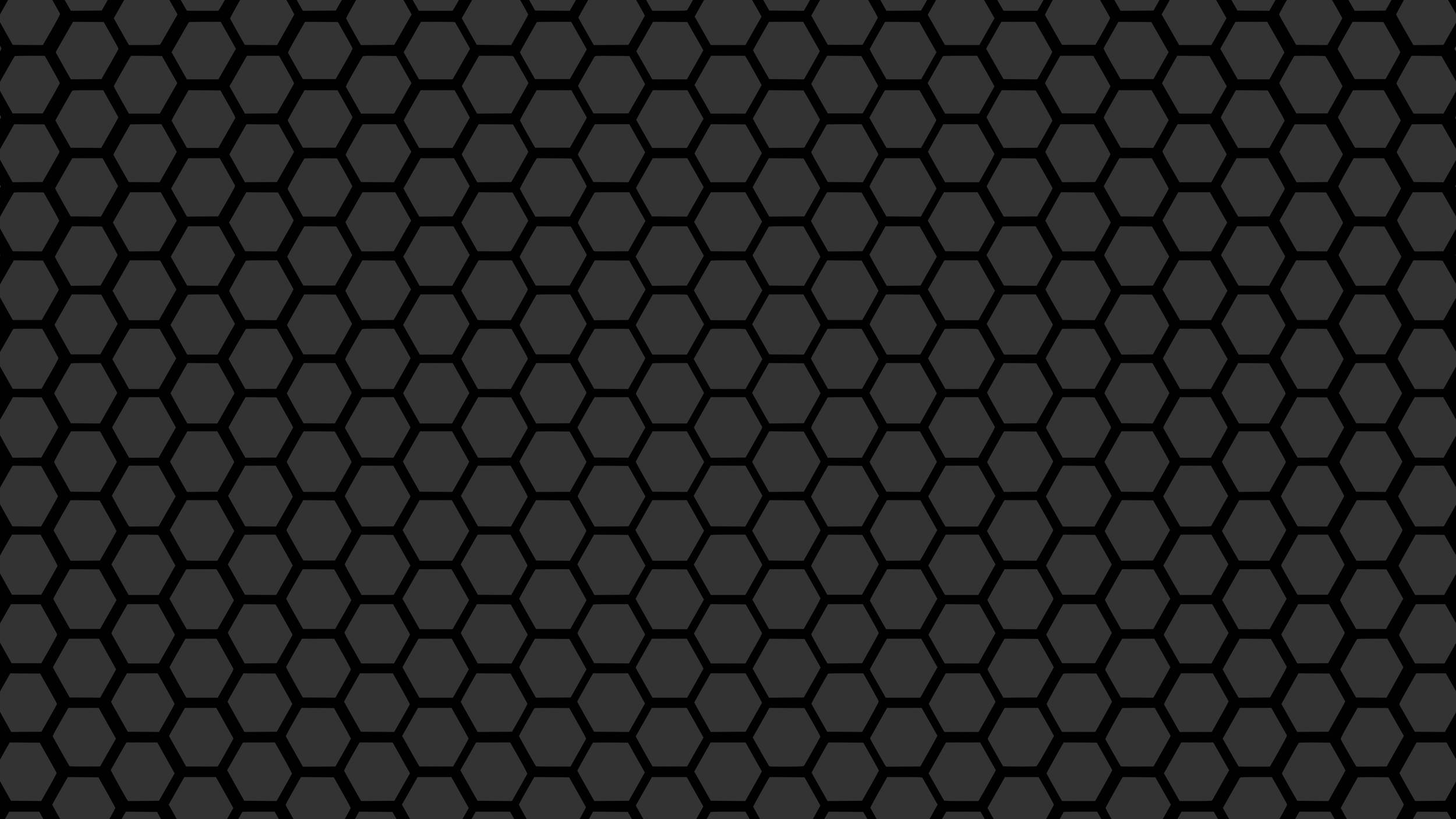
〰️
〰️
What is FDM 3D Printing?
Fused Deposition Modeling (FDM) or Fused Filament Fabrication (FFF) is one of the most common methods of 3D printing used in manufacturing various products. In FDM printing, thermoplastic filament material is melted and extruded through a small nozzle to create layers that gradually build up to form the desired object, also known as (AM) Additive Manufacturing.
---
Fused Deposition Modeling (FDM) 3D Printing
Fused Deposition Modeling (FDM) is a popular method of 3D printing that utilizes a thermoplastic filament to build objects layer by layer. Here's why FDM printing might be the right choice for your next project:
**Advantages of FDM Printing:**
1. Cost-Effective: FDM printers are generally more affordable compared to other 3D printing technologies, making them accessible for both hobbyists and professionals.
2. Wide Material Selection: FDM printing supports a variety of thermoplastic materials, including PLA, ABS, PETG, and more, offering flexibility in material properties for different applications.
3. Reliability: FDM printers are known for their reliability and ease of use, making them suitable for both beginners and experienced users.
4. Strong and Durable Parts: FDM-printed parts are typically strong and durable, making them suitable for functional prototypes, end-use parts, and mechanical components.
Disadvantages of FDM Printing:
1. Layer Lines: FDM printing can produce visible layer lines on the surface of printed objects, which may require post-processing to achieve a smoother finish.
2. Limited Resolution: FDM printers typically have lower resolution compared to other 3D printing technologies, which may affect the level of detail achievable in printed parts.
3. Support Structures: Complex geometries may require support structures during printing, which can be time-consuming to remove and may leave marks on the finished part.
Resin Printing vs. FDM Printing:
While FDM printing offers affordability and versatility, resin printing, another popular 3D printing method, offers its own set of advantages and disadvantages:
Resin Printing:
Resin printing, also known as stereolithography (SLA) or digital light processing (DLP), uses liquid resin cured by UV light to create highly detailed and smooth-surfaced objects.
Advantages of Resin Printing:
1. High Resolution: Resin printing can achieve extremely high levels of detail and surface finish, making it ideal for intricate designs and models.
2. Minimal Post-Processing: Resin-printed parts typically require minimal post-processing compared to FDM-printed parts, resulting in smoother surfaces straight out of the printer.
3. Support-Free Printing: Resin printing often allows for support-free printing of complex geometries, reducing the need for additional post-processing.
Disadvantages of Resin Printing:
1. Limited Material Selection: Resin printing typically offers a more limited selection of materials compared to FDM printing, which may restrict the range of applications.
2. Higher Cost: Resin printers and materials tend to be more expensive compared to FDM counterparts, making them less accessible for some users.
3. Messy and Hazardous: Resin printing involves handling liquid resin, which can be messy and requires careful handling due to its chemical nature.
In summary, both FDM and resin printing offer unique advantages and disadvantages, and the choice between them depends on factors such as budget, desired resolution, material properties, and application requirements.
---
This summary provides a brief overview of FDM printing, highlights its pros and cons, and briefly compares it to resin printing to help customers make informed decisions about their 3D printing needs.